CNC bending is an essential process in the metal fabrication world. Whether you’re producing complex parts for industrial machinery, automotive components, or custom designs, CNC bending can help achieve precise and consistent results. However, before you send your parts off to a fabrication shop, it’s important to understand the key factors that can affect the outcome of the process. In this blog, we’ll walk you through five critical things you need to know before CNC bending your parts.
1. Material Type and Properties Matter
The material you choose for your parts plays a major role in the CNC bending process. Different metals behave differently when subjected to bending, and understanding their properties is crucial to achieving the best results.
- Ductility and Hardness: Some materials are more flexible than others, meaning they can withstand tighter bends without cracking. For example, aluminum is known for its ductility and can handle tight bends, while materials like stainless steel are harder and may require larger bend radii.
- Springback: Materials like steel will often “spring back” slightly after bending, meaning the part may not hold the desired angle without compensation. Understanding the springback characteristics of the material you’re working with will help ensure accurate results.
- Thickness and Weight: The thickness of the material will also affect the bending process. Thicker materials require more force and may need specialized tools or machines, while thinner materials may be easier to work with but more prone to distortion.
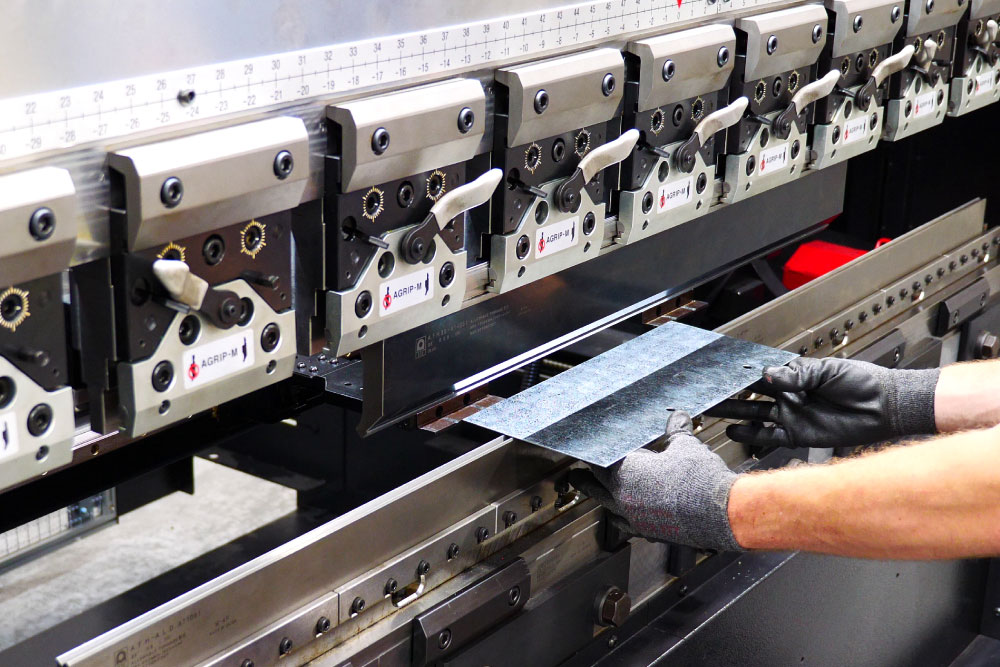
2. Know the Bend Radius and Die Selection
The bend radius refers to the inside radius of the bend, and it’s one of the most important factors to consider when CNC bending. A bend that is too tight for the material can cause cracks, fractures, or poor aesthetics.
- Choosing the Right Bend Radius: Each material and thickness will have a minimum bend radius that should be adhered to in order to avoid damage. For example, a thinner piece of aluminum can have a tighter bend radius, while thicker steel requires a larger radius.
- Selecting the Right Die: The die used during the bending process will also affect the quality of the bend. Dies come in different shapes, such as V-dies and U-dies, and selecting the right one for your material and design is essential. The die should support the material without causing excessive stress or distortion.
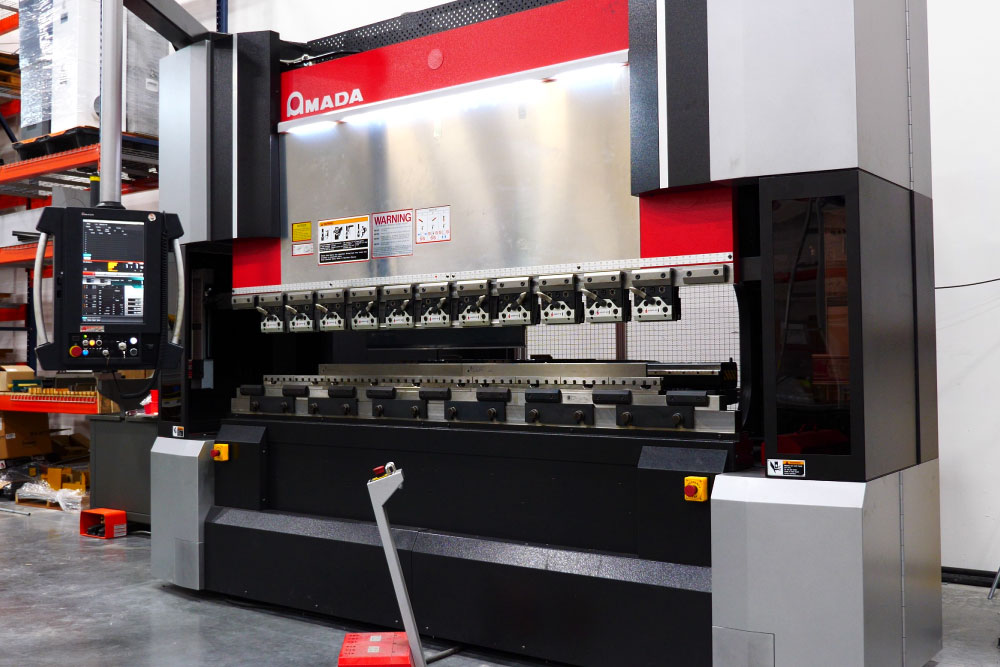
3. Understand the Bending Sequence
The order in which parts are bent can significantly impact the final product. Proper sequencing is essential for avoiding issues like warping, twisting, or distortion.
- Why the Sequence Matters: When multiple bends are required, the order in which they are performed can determine the final geometry of the part. Bending a part too early or in the wrong order can lead to misalignments or interference with previously bent sections.
- Pre-Bending and Post-Bending Considerations: For parts with multiple bends, it’s often best to start with the more complex bends first, and finish with the simpler ones. This ensures that any material deformation from the earlier bends does not interfere with the final bends.
4. Account for Tolerances and Precision
Precision is one of the biggest advantages of CNC bending, but it’s important to understand the tolerances involved in your project. Tolerances are the acceptable variations in the dimensions of the finished part, and they should be specified clearly.
- Tolerance Requirements: When sending your parts to a fabrication shop, be sure to communicate the tolerance limits required for your design. CNC bending can achieve tight tolerances, but it’s important to specify how much variation is acceptable to avoid unnecessary delays or adjustments.
- Machine Capabilities: Different CNC bending machines have different levels of precision. Be sure to discuss the accuracy and tolerances with your fabrication shop to ensure their equipment is capable of meeting your requirements.
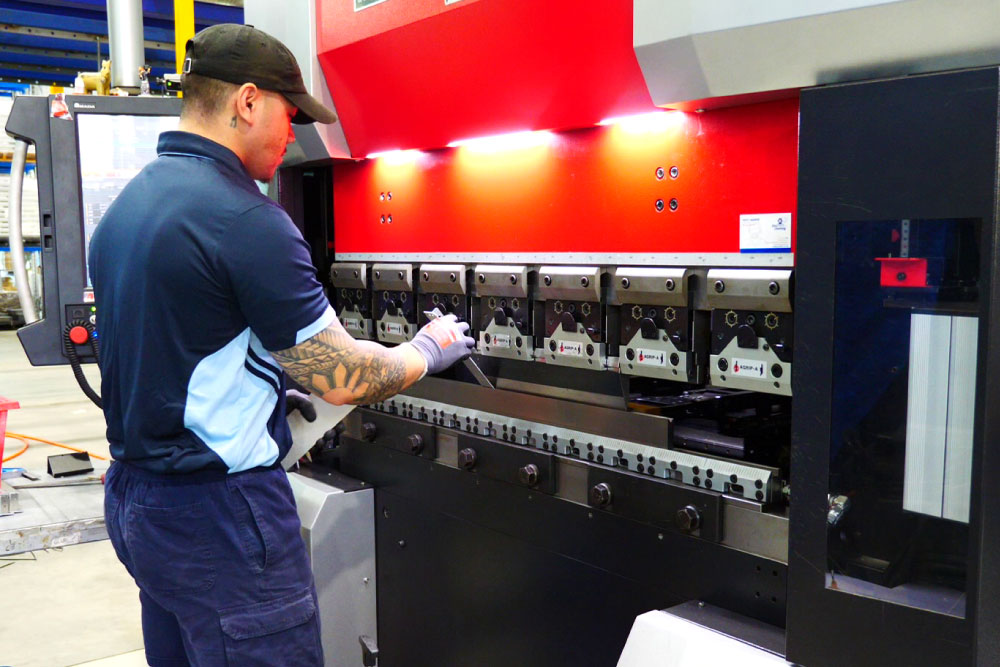
5. Consider Post-Bending Operations
Once the bending process is complete, there may be additional steps required to finish your part, such as surface treatment, welding, or assembly. Understanding these post-bending operations is key to getting the finished product that you need.
- Surface Treatment: Depending on the application, you might need to apply coatings like powder coating, anodizing, or plating to protect the metal and enhance its appearance. Some materials, such as aluminum, may require special pre-treatment or coating to achieve the desired finish.
- Welding and Assembly: In some cases, parts may need to be welded after bending, especially if multiple pieces are involved. It’s important to ensure that bending is performed in a way that does not interfere with any subsequent operations like welding or drilling.
- Inspection and Testing: After the bending process, it’s a good idea to inspect the parts to ensure they meet your specifications. Some parts may need to undergo quality control checks or testing to verify their strength, durability, or functionality.
Conclusion
CNC bending is a precise and efficient method for creating custom metal parts, but it’s essential to understand the factors that can impact the process. By considering material properties, bend radii, die selection, bending sequence, tolerances, and post-bending operations, you can ensure that your parts are produced with the highest level of quality and precision.
When planning your next CNC bending project, be sure to communicate these considerations with your fabrication shop to avoid any surprises and get the best results. A little knowledge and preparation can go a long way in ensuring your parts meet your expectations and perform flawlessly in their final application.