Powder coating is a popular and effective method for applying a durable and visually appealing finish to metal surfaces. It offers many benefits, including superior durability, resistance to corrosion, and a wide range of color and texture options. However, for powder coating to achieve the best results, it’s crucial to begin with a clean and properly prepared surface. This is where pre-treatment comes into play. Pre-treatment is an essential step in the powder coating process that directly impacts the quality and longevity of the finish. In this blog post, we’ll explore why pre-treatment is so important and how it ensures a successful powder coating application.
1. Ensures Proper Adhesion of the Coating
One of the primary functions of pre-treatment is to ensure the powder coating adheres properly to the metal substrate. A clean surface is essential for the powder to bond effectively, creating a strong and lasting finish.
- Removing Contaminants: Metals, especially those that have been handled or stored, can accumulate dirt, grease, oils, fingerprints, rust, and other contaminants. These contaminants can create a barrier between the metal surface and the powder coating, preventing the powder from adhering correctly. Pre-treatment methods, such as cleaning and degreasing, help remove these contaminants to create a pristine surface for bonding.
- Surface Activation: Pre-treatment techniques, such as acid etching or sandblasting, can roughen the surface of the metal, which helps improve the mechanical bonding between the coating and the substrate. Without surface activation, the powder coating may not fully adhere, leading to peeling, cracking, or chipping over time.
2. Improves Corrosion Resistance
One of the most significant advantages of powder coating is its ability to protect metal surfaces from rust and corrosion. Pre-treatment plays a critical role in enhancing this protective barrier.
- Removing Rust and Oxidation: Metals like steel or iron are prone to rust and oxidation when exposed to moisture or air. Pre-treatment processes, such as abrasive blasting or chemical etching, remove any existing rust or oxidation from the surface. By eliminating these imperfections, pre-treatment ensures that the coating forms an even and consistent protective layer.
- Applying Phosphate or Conversion Coatings: Many pre-treatment processes include applying a phosphate or conversion coating, such as zinc phosphate, to the metal surface. These coatings help to further enhance corrosion resistance by providing an additional layer of protection that bonds with the metal and the powder coating. This makes the finish more durable and long-lasting, even in harsh environments.
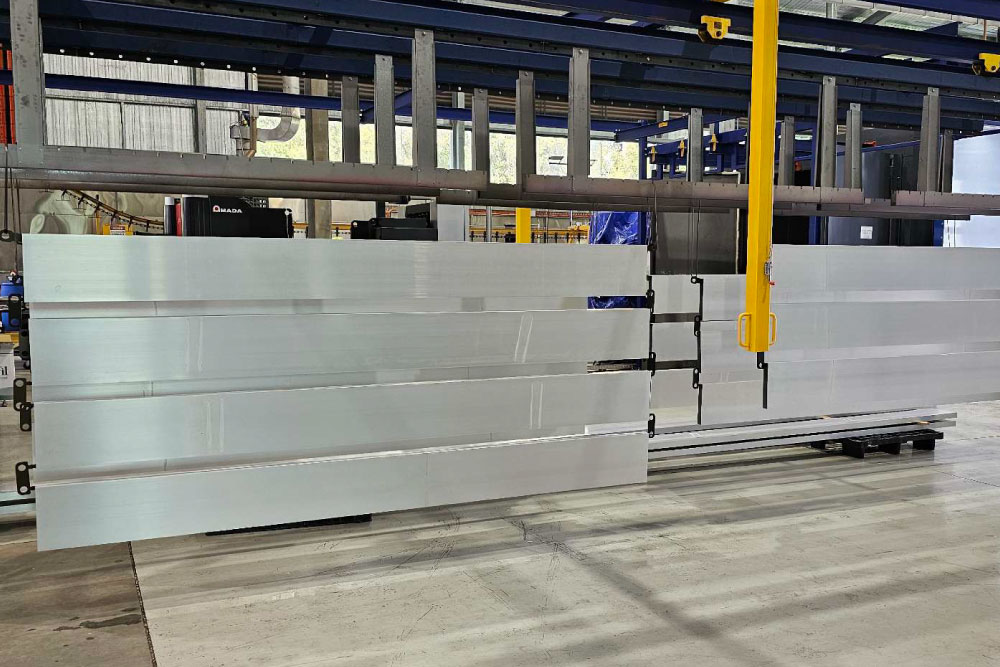
3. Promotes a Smooth and Uniform Finish
The quality of the final powder coating finish largely depends on the preparation of the surface. Pre-treatment ensures that the metal is free from imperfections and inconsistencies, which can affect the overall appearance of the coating.
- Removing Surface Imperfections: Metal surfaces can have scratches, burrs, or other imperfections that could affect the powder coating process. Pre-treatment steps such as sandblasting, shot blasting, or chemical cleaning help eliminate these flaws, creating a smoother surface for the powder to adhere to. This results in a more uniform, aesthetically pleasing finish.
- Preventing Orange Peel Effect: Without proper pre-treatment, the powder coating may not lay down evenly, resulting in an undesirable texture known as “orange peel.” Pre-treating the surface helps eliminate the risk of this texture, ensuring that the final finish is smooth and consistent.
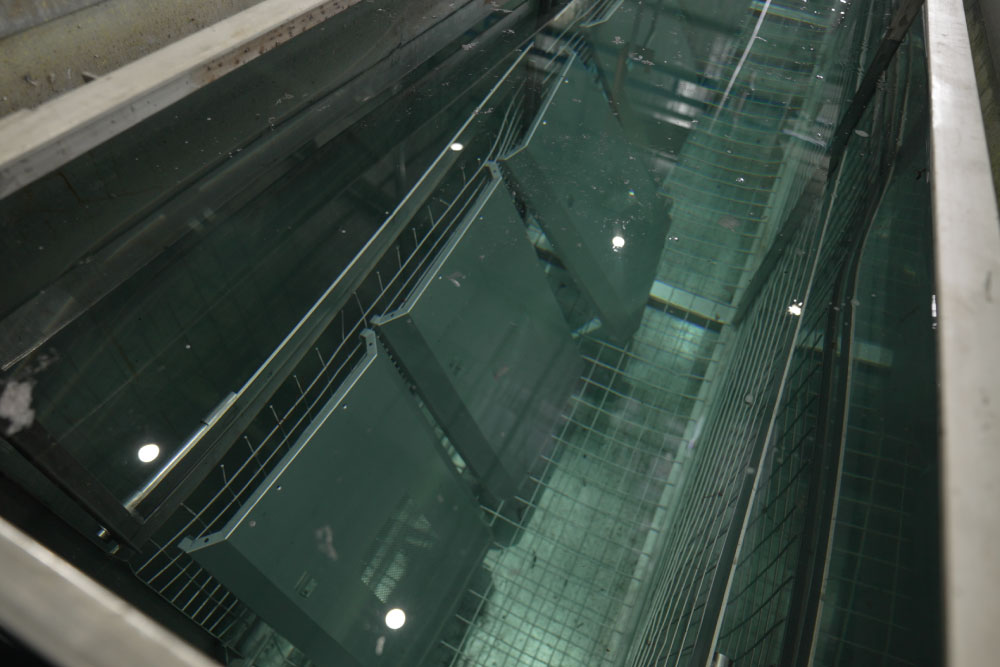
4. Enhances Durability and Longevity of the Coating
Proper pre-treatment not only improves the appearance of the powder coating but also contributes to its long-term performance. A well-prepared surface allows the powder coating to cure more effectively and results in a stronger, more durable finish.
- Reducing the Risk of Delamination: Delamination occurs when the coating fails to bond properly with the substrate, often due to contaminants or inadequate surface preparation. Pre-treatment removes oils, dust, and debris that can interfere with the coating’s ability to bond, significantly reducing the risk of delamination.
- Ensuring Consistent Curing: Pre-treatment also ensures that the surface is prepared to withstand the curing process. Metals with contaminants or oxidation can interfere with how the coating cures, leading to issues like poor adhesion or an uneven finish. Pre-treatment ensures the surface is uniform, allowing the coating to cure evenly and bond properly, leading to a finish that will last longer and withstand wear and tear.
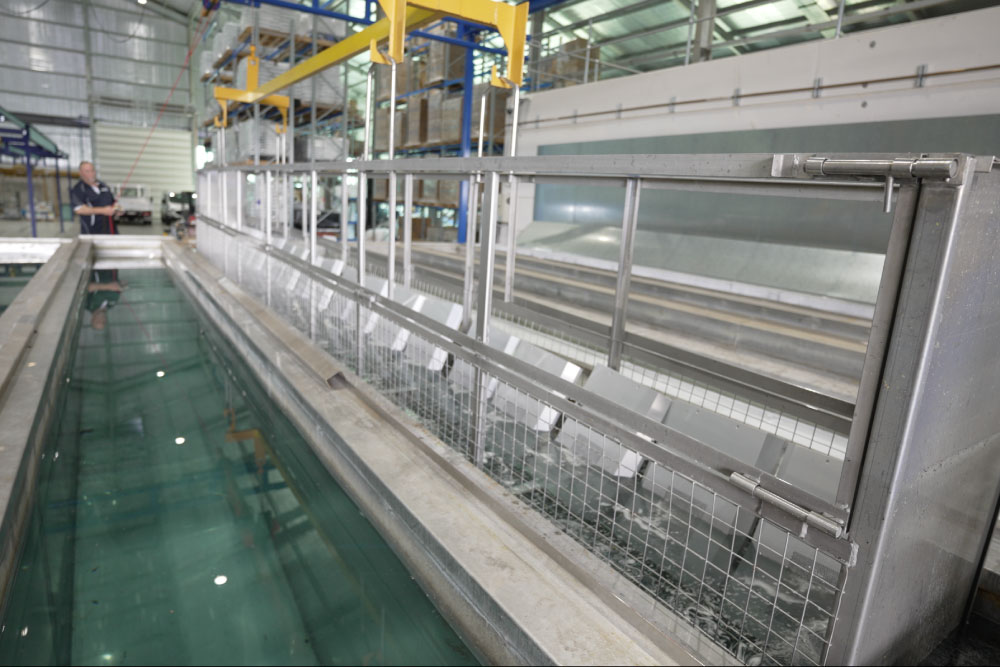
5. Reduces the Risk of Defects and Inconsistencies
Without proper pre-treatment, the risk of defects in the powder coating increases. These defects can range from bubbles and blisters to peeling and discoloration. In some cases, improper preparation can result in a coating that looks good initially but fails prematurely.
- Prevents Contamination During Application: During the powder coating application process, if the metal surface is not properly cleaned and pre-treated, airborne contaminants such as dust, oils, or dirt can settle on the surface and interfere with the coating. This can result in defects like fisheyes (small craters on the surface) or poor adhesion. A thorough pre-treatment process ensures the metal is free of any potential contaminants that could affect the quality of the finish.
- Minimizes Bubbles and Blisters: When metal parts are not properly pre-treated, moisture or gas trapped under the coating can lead to bubbles or blisters. Pre-treatment eliminates contaminants and moisture, reducing the likelihood of these defects and ensuring a smooth, flawless finish.
6. Increases Environmental and Health Safety
In addition to its performance benefits, pre-treatment can also contribute to a safer and more environmentally friendly powder coating process.
- Minimizing Harmful Chemicals: By properly preparing the surface, the need for harmful chemicals or excessive abrasive materials is minimized. This reduces the environmental impact and the risks associated with using harsh chemicals, creating a safer workplace.
- Improved Waste Management: Pre-treatment processes, such as washing or phosphate coating, often use water-based or eco-friendly solutions that can be recycled or safely disposed of, contributing to a more sustainable powder coating process.
Conclusion
Pre-treatment is an essential step in the powder coating process that should never be overlooked. From ensuring proper adhesion and corrosion resistance to promoting a smooth and uniform finish, pre-treatment directly impacts the quality, durability, and longevity of the powder coating. By thoroughly cleaning, activating, and conditioning the surface, pre-treatment creates the ideal foundation for a high-quality and long-lasting finish.
If you’re working with a fabrication shop or powder coating provider, make sure they use proper pre-treatment techniques and equipment to ensure the best results. A good pre-treatment process not only improves the appearance of your parts but also enhances their overall performance, helping your powder-coated items withstand wear, tear, and environmental exposure for years to come.